Exploring the World of Plastic Molding Injection in Metal Fabrication
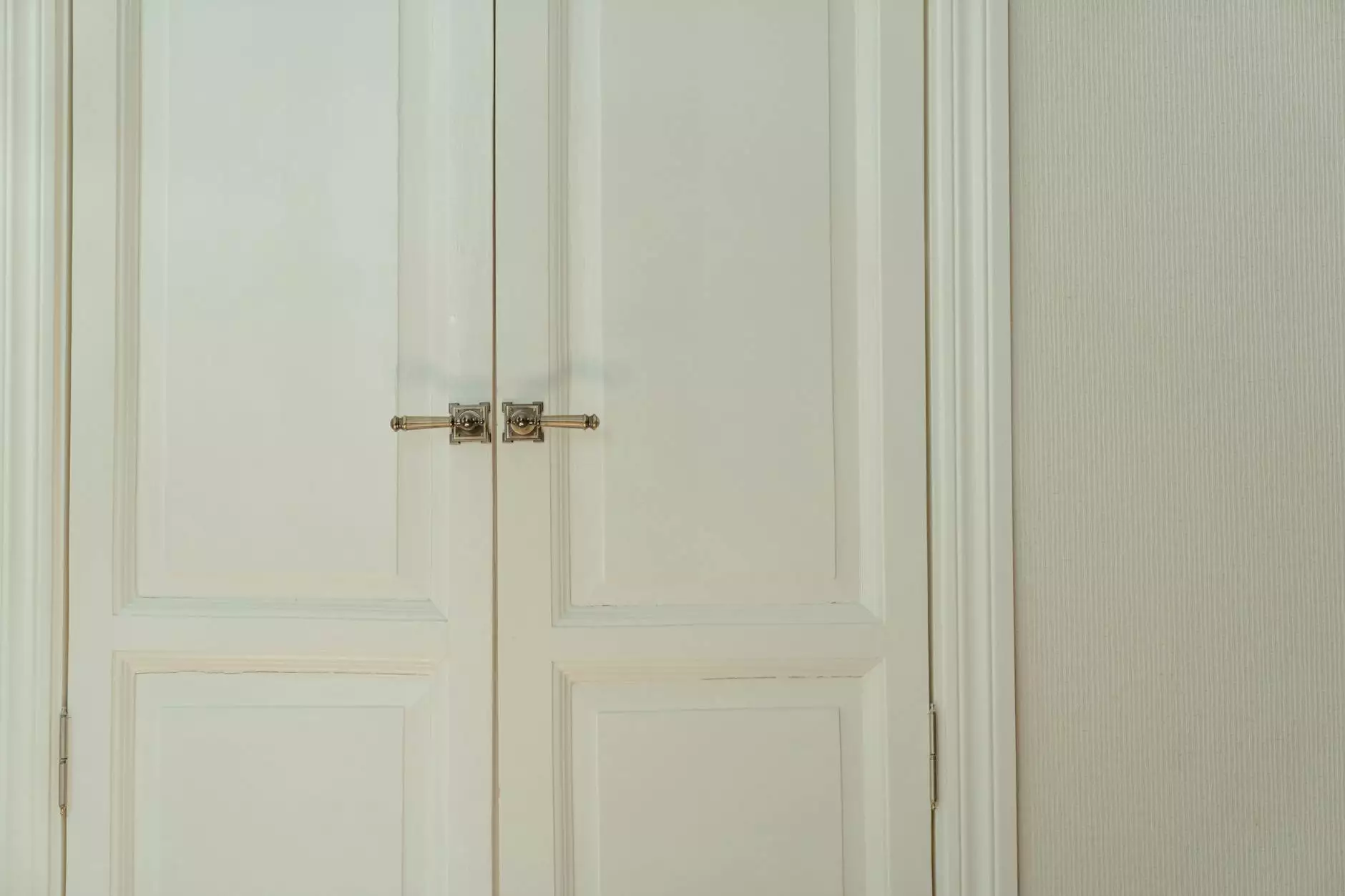
In today's rapidly evolving manufacturing landscape, plastic molding injection has emerged as a crucial technology within the metal fabrication industry. This advanced technique is not only transforming how products are made but is also influencing the efficiency and creativity of design processes across various sectors. In this comprehensive article, we will delve deep into the intricacies of plastic molding injection, its benefits, applications, and its significant role in enhancing manufacturing capabilities.
Understanding Plastic Molding Injection
Plastic molding injection is a manufacturing process that involves the production of parts by injecting molten plastic into a mold. This method allows for high precision and the ability to produce a large number of parts in a relatively short amount of time. The process can be used for a wide range of materials, including various types of thermoplastics, which offer distinct advantages in terms of flexibility, durability, and weight.
How the Process Works
The plastic molding injection process consists of several key stages:
- Material Preparation: The process starts with the selection of the appropriate plastic resin, which is then heated until it becomes molten.
- Injection: The molten plastic is injected into a pre-designed mold under high pressure.
- Cooling: Once the mold is filled, the plastic cools and hardens to take the shape of the mold.
- Demolding: After sufficient cooling time, the mold is opened, and the solidified part is removed.
- Post-Processing: Depending on the requirements, additional finishing processes like trimming, sanding, or painting may be applied.
Advantages of Plastic Molding Injection
One of the reasons for the widespread adoption of plastic molding injection in the metal fabrication industry is its numerous advantages:
- Cost-Effectiveness: This process is highly efficient and can produce large volumes of parts at a lower cost per unit compared to other manufacturing methods.
- Design Flexibility: Designers can create complex geometries and intricate details that are often impossible to achieve with traditional metal fabrication techniques.
- Quality and Precision: The injection molding process allows for tight tolerances and a high level of consistency across production runs.
- Material Variety: A wide range of materials can be used, allowing manufacturers to select the best option for their specific application.
- Reduced Waste: Since the amount of material used can be precisely controlled, there is minimal waste generated during production.
- Speed: The process is incredibly fast, with the ability to produce thousands of parts in a matter of hours.
Applications of Plastic Molding Injection in Metal Fabrication
The versatility of plastic molding injection extends across many industries, showcasing its wide array of applications:
1. Automotive Industry
The automotive sector heavily relies on plastic molding injection for producing a multitude of components, including dashboards, panels, and under-the-hood parts. This not only helps in reducing vehicle weight for enhanced fuel efficiency but also allows for greater design flexibility and improved aesthetics.
2. Electronics
In the electronics industry, plastic molding injection is utilized to create housings and components that protect sensitive electronic parts. The process enables manufacturers to produce lightweight, durable casings with intricate designs that facilitate functionality while maintaining a sleek appearance.
3. Medical Devices
The medical field benefits from plastic molding injection through the production of high-precision components used in devices such as syringes, surgical instruments, and diagnostic equipment. The ability to create complex designs with stringent quality standards is crucial for ensuring safety and efficacy in medical applications.
4. Consumer Products
Everyday items such as toys, kitchenware, and personal care products are often manufactured using plastic molding injection. This process allows brands to quickly bring innovative designs to market while maintaining cost efficiency.
Challenges and Considerations
Despite its many benefits, the plastic molding injection process does come with challenges that businesses need to consider:
- High Initial Costs: The cost of creating molds can be significant, which may deter smaller companies from utilizing this method for low-volume production.
- Material Limitations: Not all types of plastic are suitable for injection molding, and selecting the wrong material can lead to product failures.
- Design Complexity: While the process allows for intricate designs, overly complex molds can lead to increased production time and costs.
- Environmental Impact: The production and disposal of plastic can raise concerns about sustainability and environmental health, which industries are increasingly addressing through recycling and biodegradable materials.
Innovations in Plastic Molding Injection
The field of plastic molding injection is constantly evolving, with innovations aimed at improving efficiency, sustainability, and overall quality. Some key trends include:
1. Industry 4.0 Integration
The integration of IoT (Internet of Things) into production processes is paving the way for smarter manufacturing. By leveraging data analytics, manufacturers can optimize their injection molding processes, reducing waste and enhancing efficiency.
2. Development of Biodegradable Plastics
With growing concerns about plastic waste, notable advancements have been made in developing biodegradable materials suitable for injection molding. This not only addresses environmental issues but also meets the demands of eco-conscious consumers.
3. Advances in Mold Technology
New technologies such as 3D printing for mold creation allow for rapid prototyping and reduced mold production time. This innovation is making plastic molding injection more accessible for short runs and customized parts.
4. Automation and Robotics
Incorporating automation in plastic molding injection processes leads to enhanced efficiency, reduced labor costs, and higher precision. Automated systems can monitor production processes and adjust parameters in real-time, ensuring optimal performance.
The Future of Plastic Molding Injection
The future of plastic molding injection in metal fabrication is promising, with ongoing advancements poised to revolutionize how products are designed and manufactured. As the demand for lightweight, durable, and cost-effective components continues to grow, industries will increasingly turn to this technology.
Conclusion
In conclusion, plastic molding injection stands out as a pivotal innovation in the metal fabrication industry, providing numerous advantages and applications across multiple sectors. Companies like Deep Mould are at the forefront of this technology, leading the charge towards more efficient and sustainable manufacturing practices. Understanding the intricacies of this process not only helps businesses leverage its benefits but also prepares them for the future of advanced manufacturing.
By investing in plastic molding injection, industries can not only meet the demands of today’s market but also pave the way for a more innovative and environmentally friendly tomorrow.